Raft Molding
Mold intelligent manufacturing
Here is the placeholder text
Here is the placeholder text
Here is the placeholder text
Here is the placeholder text
Here is the placeholder text
Here is the placeholder text
Here is the placeholder text
Here is the placeholder text
Here is the placeholder text
Here is the placeholder text
Here is the placeholder text
Here is the placeholder text
Part Design
Rapid prototyping
Part analysis plays a critical role in the whole project. Bringing a concept design into real life product requires feasible structures that could be applied to massive production. An excellent structure design will not only guarantee a smooth production, but also lower the costs of tooling &assembly.
In Hoki, before we start to design molds in every project, a detailed DFM report made by our structural engineer will be sent to you, giving professional suggestions to help you to improve your project together.



Our engineers have many years of technical experience in mold design and mold manufacturing process; and have professional design guidance from our foreign offices!

Using advanced computer-aided technology, our professional and experienced engineers focus on designing customized products and other high-precision molds.

2D mold assembly drawings will be completed and submitted to the customer for approval within 3 to 4 working days.

Detailed 2D mold parts drawings of all work will be completed and sent to the customer before the mold is shipped.

The complete 3D model of the mold, including front and rear mold cores, A and B plates, sky surface and bottom plate, will be completed and sent to the customer before the mold is delivered to the customer.
RP / 3D printing
Rapid prototyping
Using rapid prototyping is a wise choice to materialized your idea before you put it into massive production. It shortens the product R&D cycle, lower production costs and improve efficiency. We are familiar with 3D printing ways like FDM, SLA, 3DP, DLP etc., this could help you with a quick review of appearance, assembly and find the defects at the early stage of product development.

Tooling Optimization
Mold optimization
The result of plastic injection molding could be effected by many factors, which leads to the complexity of tooling design work.
To design and manufacture an injection mold is more like starting a mysterious journey with art and science.
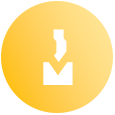
Mold Flow Analysis
It is the most effective way to find potential problems during injection before building molds.
The materials used in molding can vary in fluidity, rigidity, pliability etc., they behave and respond differently when they are injected to the mold, the results from their mold flow analyses can help us to predict any complications that might encounter. Ultimately, these analyses will benefit the selection of injection gate, runner type, air vent design etc. to the mold.
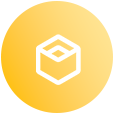
Mold Structure Optimization
For a smooth mass production at its best efficiency, the mold structure should got not only a well movement but also a design under the principles of the lowest fault level, the shortest molding cycle, the longest mold life, etc. At Hoki, your every mold will be deeply customized following your requests, together with specified part conditions and the most optimized structure, which finally enables your mass production to be at a higher efficiency and a lower costs.
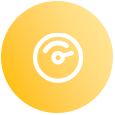
Conformal Cooling
The cooling time occupies about 50-60% of the whole molding cycle, a well-proportioned and logical cooling system can maintain the best dimensional stability and minimum deformation of the part after demolding. A terrible cooling lines design directly leads to a serious part quality problem and even mold life. We use a conformal cooling system by adopting various methods of cooling to make sure every hot spot in the mold could be eliminated properly.
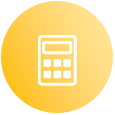
Cost Effective
Each mold is deeply customized, and each customer got their own specific requirements and budget for the molds. With our rich experiences of service in injection mold design and manufacturing for a number of areas, on the basis of meeting your standards of producing qualified parts, we can offer flexible customization choices according to your budgets, to help you with costs control.
Narrow Tolerance
Narrow Tolerance
Machining Capability
Our company has adopted many advanced machining equipment for every machining step, ranging from five axis high-speed milling, five axis gun drilling, to precision electric discharge etc. And still keep introducing new machines to the list.
Our mold machining capacity covers from 300x300 mm to 3000x2200 mm.
Part ranging: 20g to 20000g in injection volume.

Maximum processing capacity: 2500X2200X1250(mm)
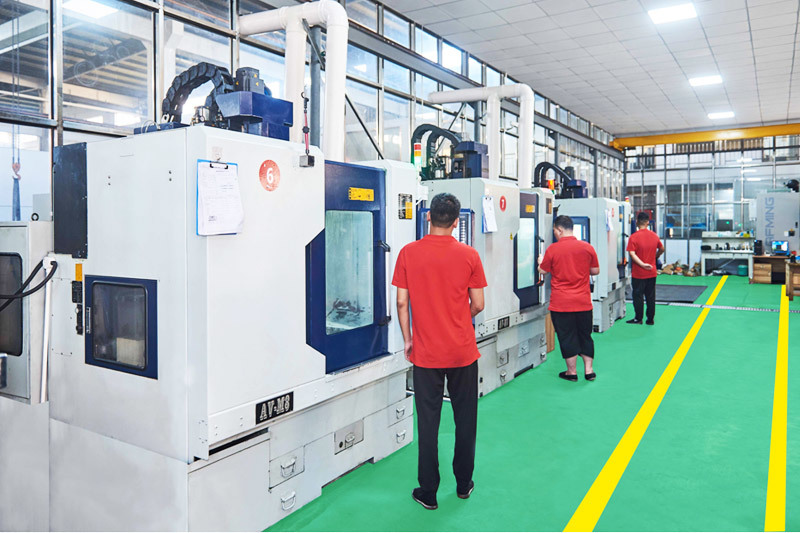
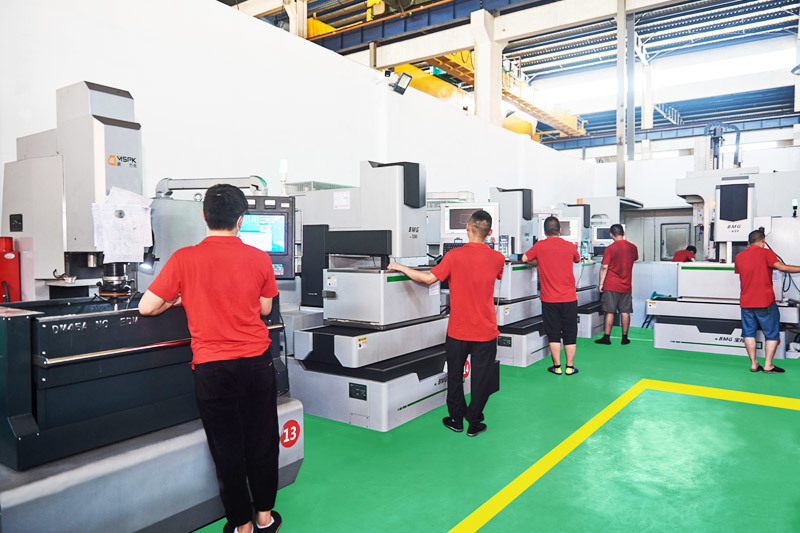

Accuracy Inspection
Accuracy Inspection
After finishing the CNC machining of the core and cavity in the mold, there might be still some inserts or complex curved surfaces need to be formed by technique like EDM, then the tolerance of the electrodes is with great importance.
By adopting of three-coordinate measuring machine (CMM), we can make a compare of the positions, sizes, curved lines &surfaces from the 3D digital data with the machined mold parts, and it comes with a graphical report that enable us to have a visual and clear overview of the tolerance of the mold.



Process optimization
Process optimization
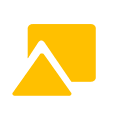
Correct Materials
Different plastics have various chemical properties. It is very important to choose the right mold steel for your plastic material. With the rich experiences we have gained after deeply involved in the industry for so many years, we have a deep understanding of choosing the most suitable steel and its process technique to meet the requirements of various plastics. At Hoki, a wide range of steel materials are available, you can easily find your preference or select from our suggestions.
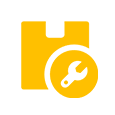
Correct Processes
Different mold requirements are in various machining needs. To choose the right process techniques and sequence play a critical role in making manufacture plan, not only will it have influence on the machining tolerance, but also the whole project schedule. At the beginning of each project, our technicians will call a special meeting to determine the most suitable machining techniques and their sequence to ensure the tolerance of the mold manufacturing.
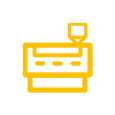
Correct Conditions
Apart from its mold, the quality of the part has deep connection with injection conditions as well. Some plastics are sensitive to humidity, while some ones could easily be affected by temperature, and some ones behave differently under different pressure. Then approaches to cope with this situation should be carried out accordingly. At the mold trial stage, we will collect the forming conditions, adjust them accordingly to get a qualified part. These conditions will be provided to you to start MP as soon as possible.